Strategy
Mitigation
Minimize Embodied Carbon
Even before a project is built, the manufacturing, transportation, and construction of materials contribute to a it's embodied carbon. This can be reduced by sourcing materials locally, reusing on-site materials, or choosing materials that require less intensive manufacturing.
Limit demand for new material
Options
...by building less.
...by reusing on-site materials.
...by using natural materials rather than ones manufactured and brought to the site.
…by siting development in the project site near to existing infrastructure tie ins.
…by reducing redundancies.
…by using the maximum allowable spacing of welded wire fabric or textile reinforced concrete instead of rebar.
…by using salvaged materials from regional demolition projects or salvage yards
…by limiting waste using minimal cuts, prefab, or dimensioned materials.
Case Study
For a decommissioned airport turned into Ellinikon Park, Sasaki reused approximately 300,000 sq ft of concrete from the runways. Because the 30” thick slabs were poured with golf ball sized marble aggregate and no rebar, various treatments were used to reveal the texture for applications in fountains, retaining walls, furnishings, and hardscape.
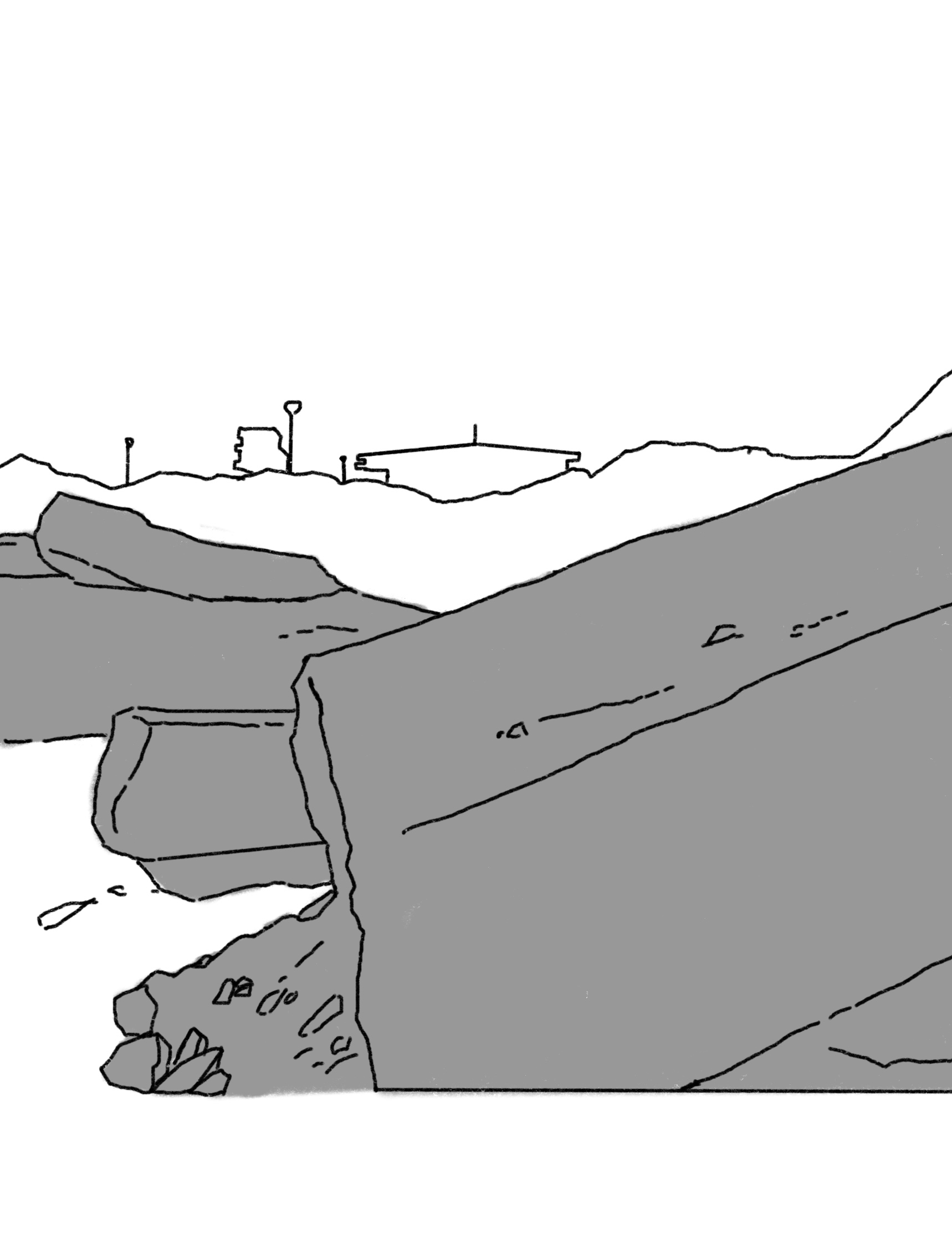
Choose materials with less energy-intensive manufacturing
Options
…such as alternative material(s) to concrete for hardscape.
…such as lower-carbon concrete.
…such as steel with a high percentage of recycled content.
…such as steel from electric arc furnaces and manufacturers powered by renewable energy.
…such as recycled materials.
…such as engineered wood fiber instead of wood chips or rubber surfacing for play areas.
…such as lightweight fill for green roofs instead of foam or cellular concrete.
…such as rammed earth walls or wood fences instead of metal fences of concrete walls.
Case Study
In San Bernadino, a city in southern California, the Unified School District decided to use 13 outdoor furnishing product types from the manufacturer Vestre in 69 schools. The SSAB-produced steel in these products has 30% lower emissions than average, produced by SSAB with fossil-free hydrogen, and soon by electric arc furnaces. The two Vestre factories are powered by 100% renewable electricity in part by onsite solar.
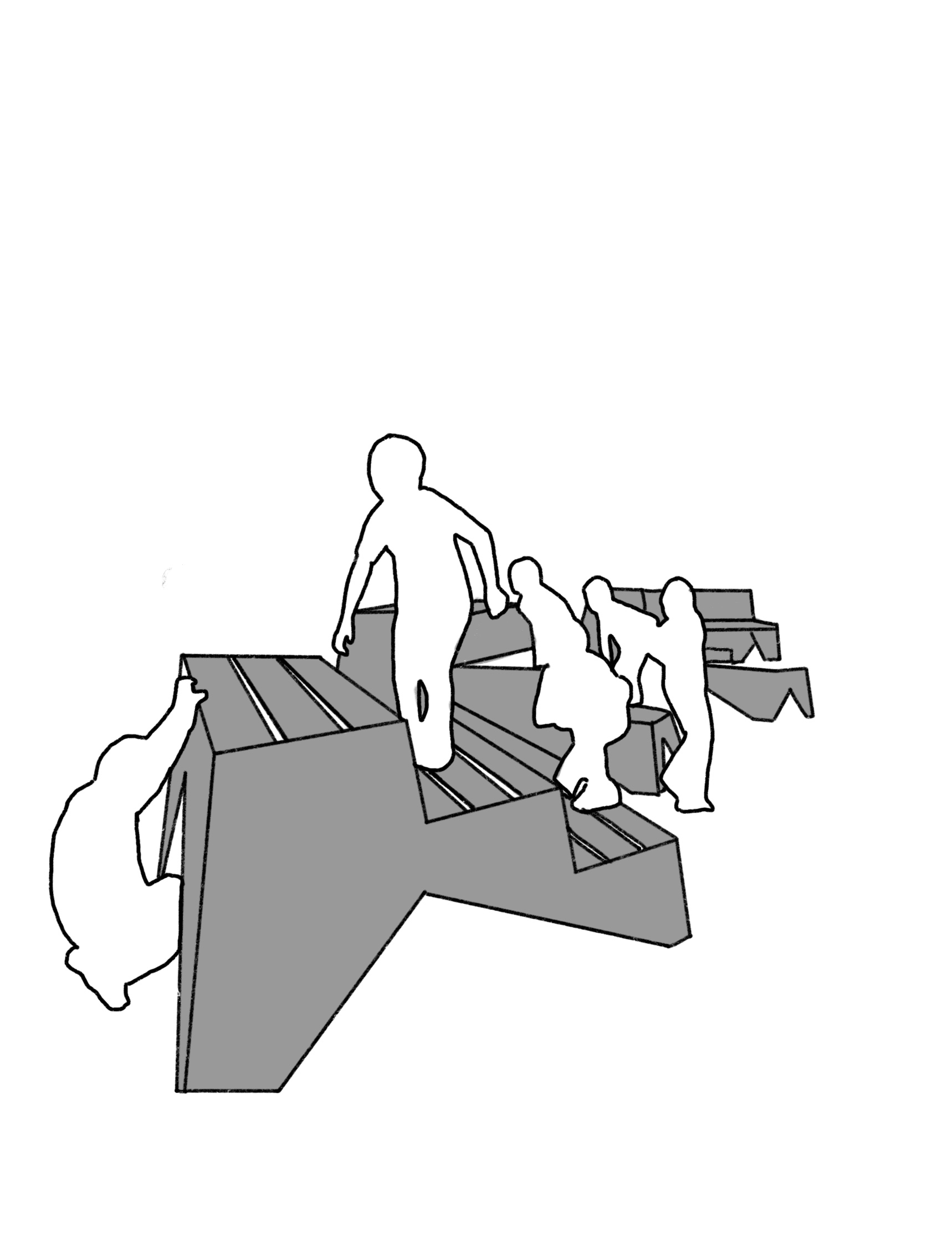
Choose materials with less energy-intensive machining/finishing
Options
…such as monolithic wood seating.
…such as natural stone.
Case Study
For the Broad Museum’s 24,000sq ft public outdoor space, Hood Design Studio created monolithic wood for seating elements. The seats and tables were made with simple cuts to salvaged Barouni olive tree trunks. The gnarled forms match the 100-year-old olive trees planted in the plaza.
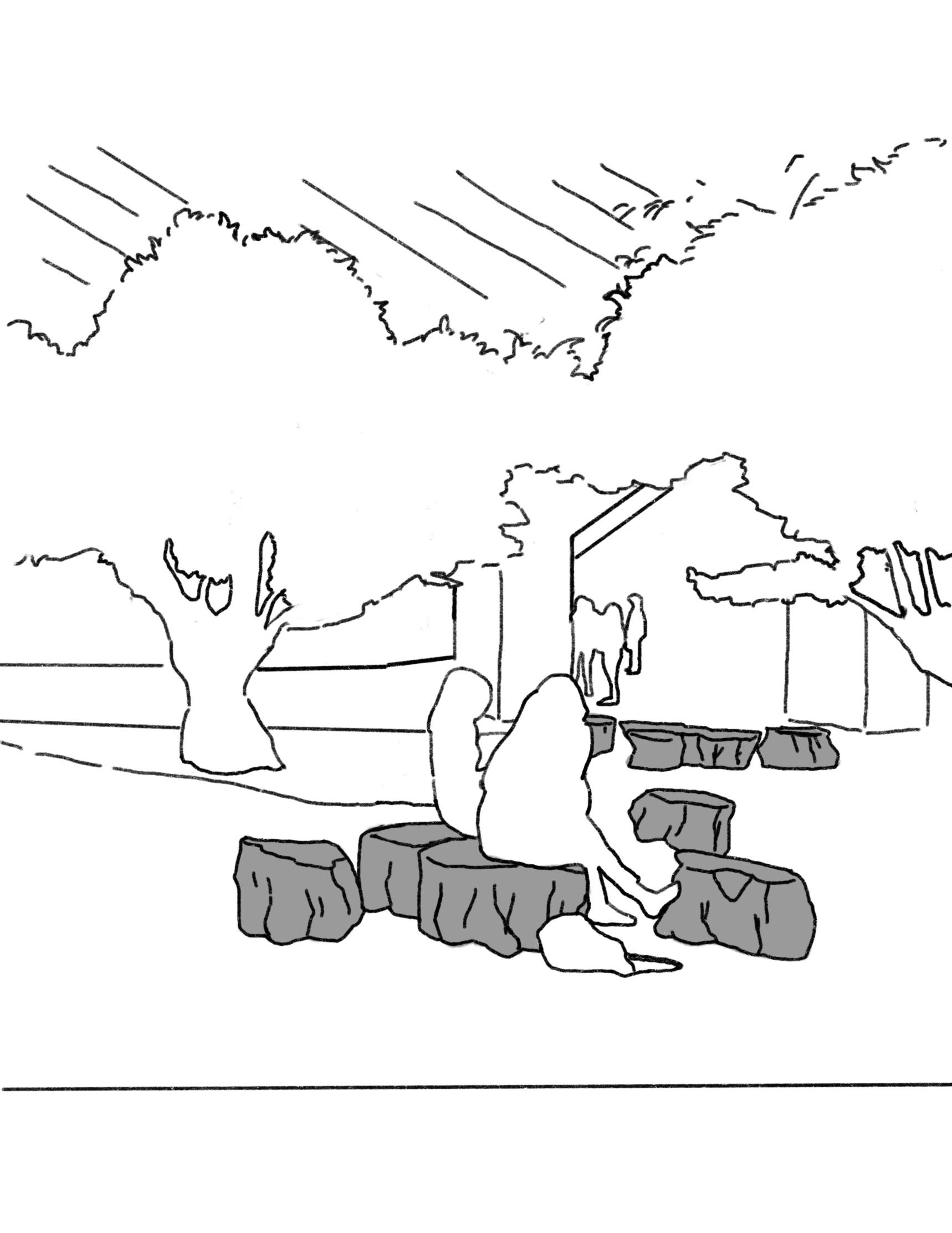
Source materials and fabricate regionally (within the state or province)
Options
Case Study
For site furnishings at the Presidio Tunnel Tops, Field Operations designed sculpted benches made from a 40,000lb, 90ft Monterey Cypress tree that had fallen at the old Army base during a winter storm, but had not been recovered. The logs were milled an hour north and brought back to the city for curing and assembly, then installed at the new park. From tree to bench, total transport was only 100 miles, or less than three hours driving time.
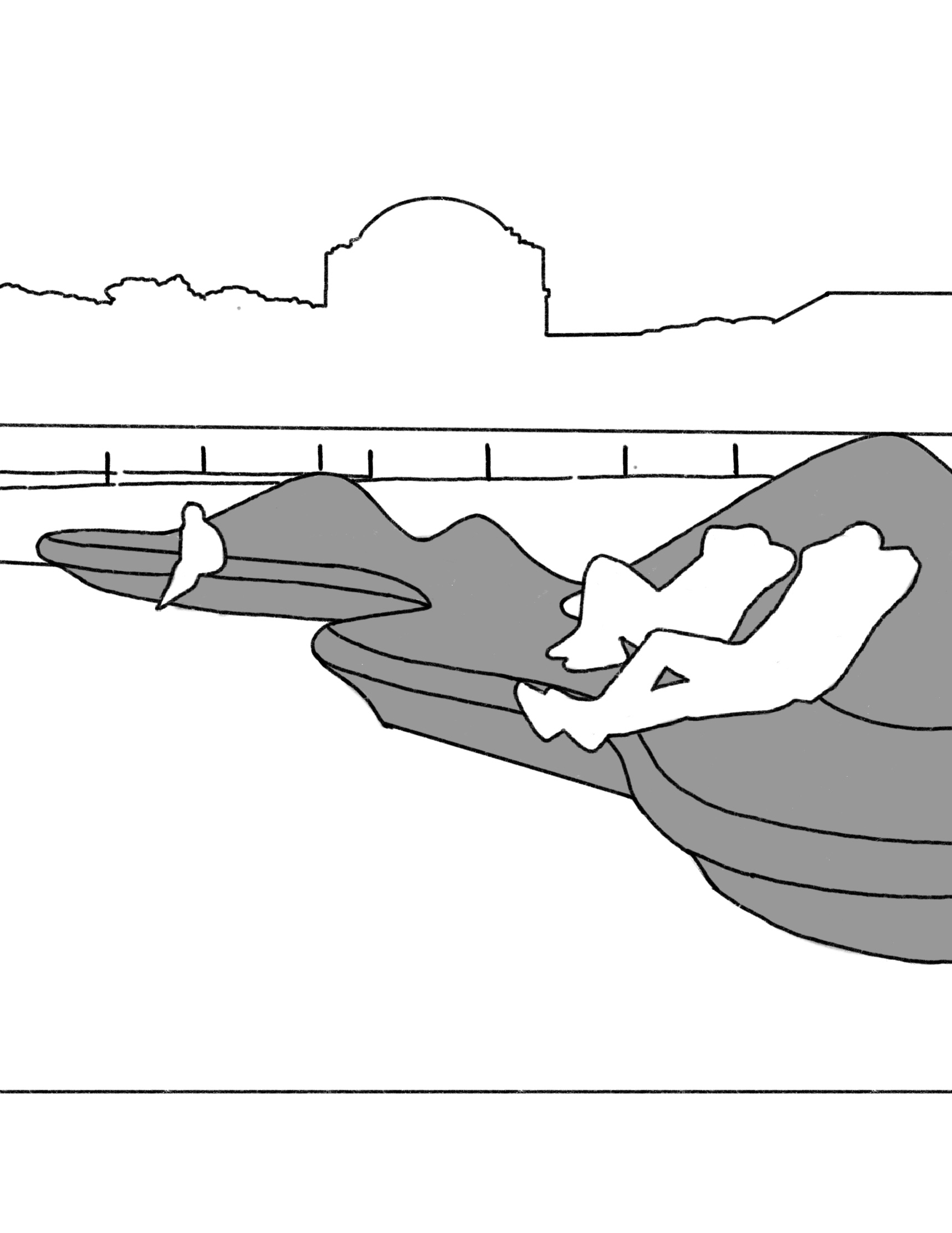
Design for deconstruction and material reuse
Options
…with fasteners (mechanical instead of adhesives, visible, few, or none).
…with simple components, modules, and fewer larger elements.
…with materials (high worth, low variety, no composites).
Case Study
Walking Wall is a 500-yard art piece by Andy Goldsworthy at the Nelson-Atkins Museum of Art. It is composed of stones freshly quarried, dug from fields, and reclaimed from old prairie walls and dry stacked four feet high by skilled wallers. The modularity of the wall is on display as it “walks”—being disassembled on one end, moved piece by piece, and assembled on the other end. A single material and no binders allow the components to be reused over and over.
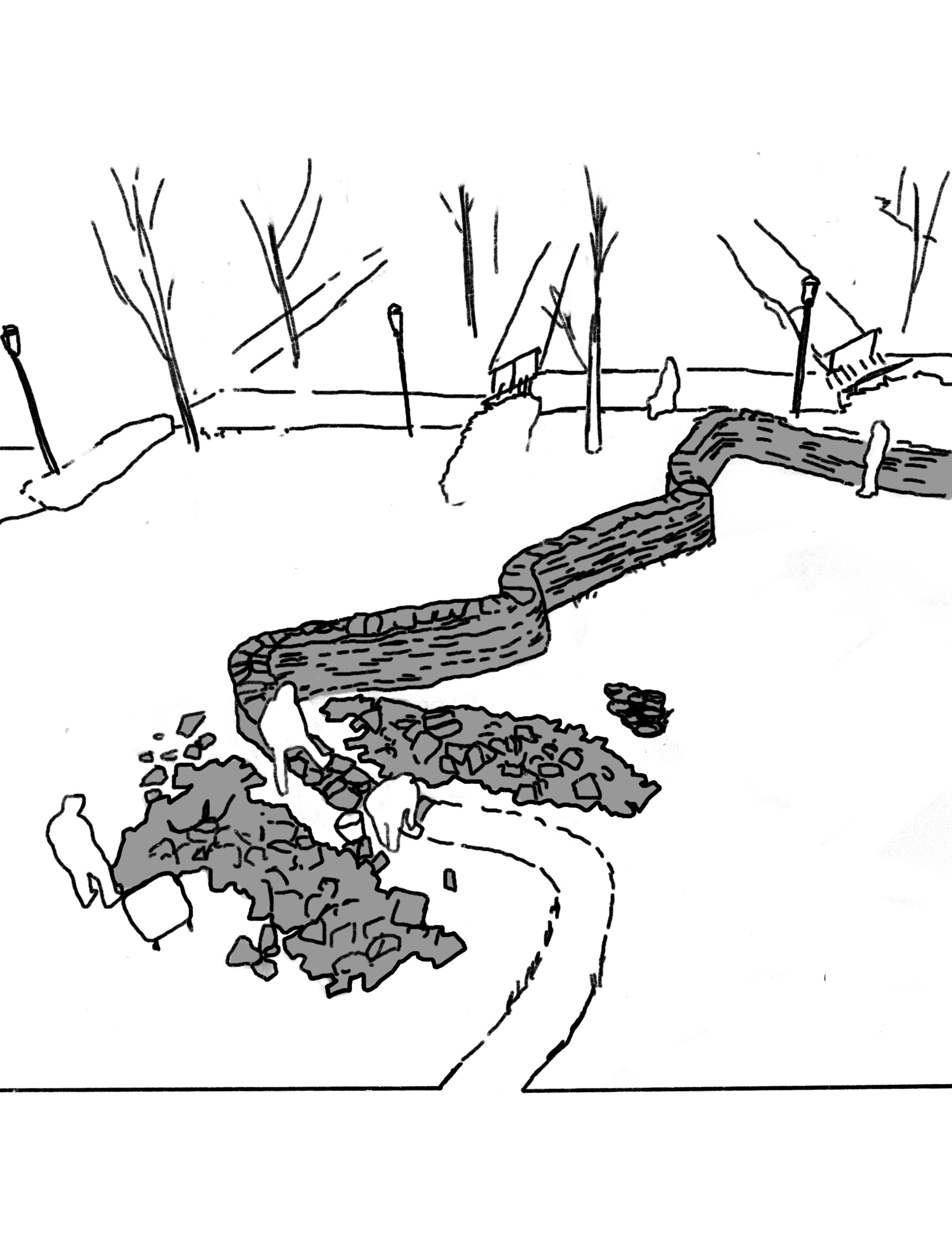
Keep everything on site (no off hauling to landfill)
Options
…by retaining fill; cap contaminants, balance cut/fill operations.
…by incorporating demolition waste (inorganic).
…by incorporating tree debris (organic).
Case Study
Cator Park is a new 8-hectare park on the site of a 70s-era suburban public housing complex (council estate). The last of the concrete brutalist buildings were demolished in 2013 as a part of urban renewal (regeneration). HTA Design used 30,000 cubic meters of construction and demolition debris to make landforms. They were thus able to limit emissions involved in off hauling to a C&D landfill. In total 98% of the rubble is being recycled or reused on site.
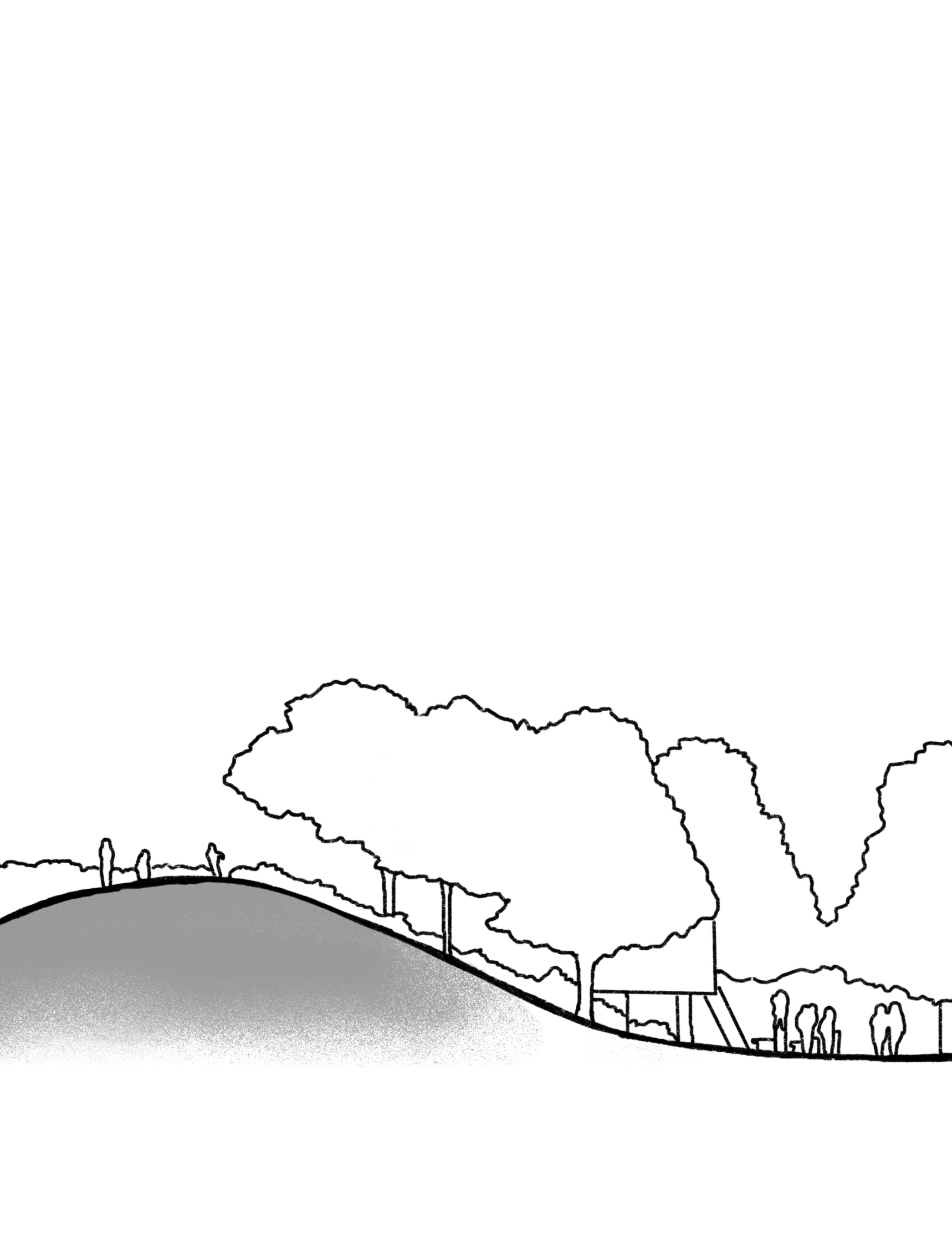
Design to limit construction vehicle hours
Options
…by limiting grading, earthwork, and/or cut/fill operations.
…by limiting trenching, excavation, drainage, and subgrade work.
…by limiting paving.
…by limiting grubbing and land clearing.
Case Study
SmithGroup redesigned an abandoned rail corridor that ran through the center of Detroit into Dequindre Cut Greenway. Built out in two phases, the cut refers to a 25’ below grade trench. Repurposed for the greenway, the trench involved comparatively minimal grading, considering the 50’ width. Operations mostly focused on clearing trash and brush, revealing the old bones of the retaining walls and old bridge abutments.
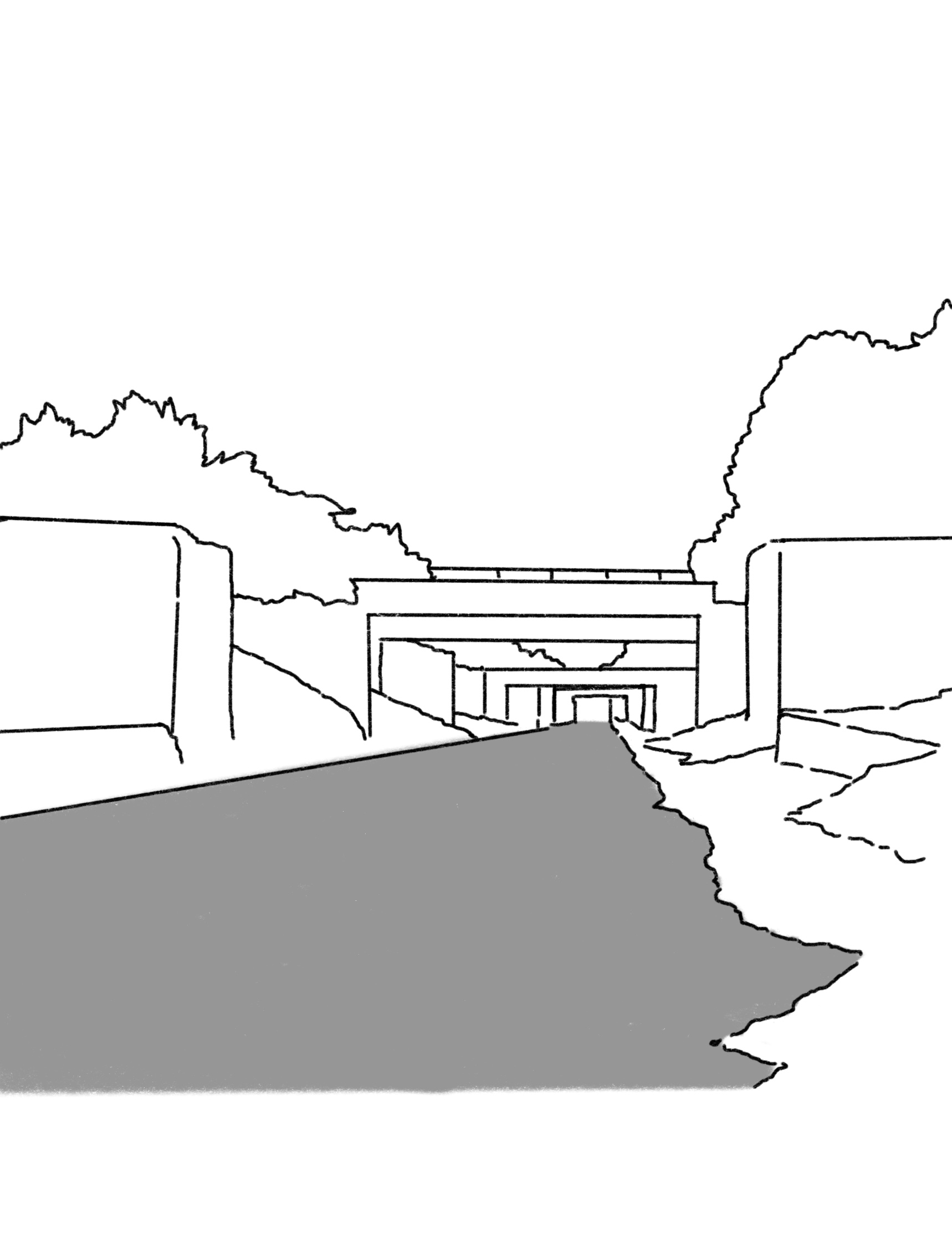